
Forging Press
Hamamatsu Tekko has built a fully equipped
system, including a 630 t press in Japan. At our
overseas factories, we have installed even larger
800 t ma chine s , expanding our r ange of
production. We have also worked to reduce costs
by installing automatic transfer machinery.
We have furthermore expanded everything from
design to coarse material completion to in-house
production, establishing a system that can meet
customers' needs with advanced technological
capabilities.
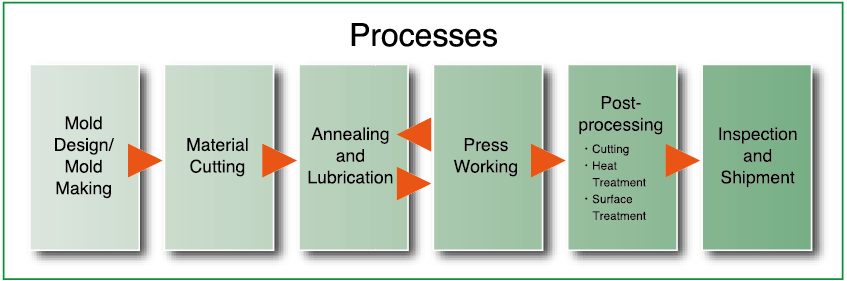
Parts Former (Horizontal Multi-Stage Forging Machine)
Equipment owned by PT.HAMATETSU INDONESIA
A parts former uses its built-in cutting mechanism to cut wire (coil) materials into it to a certain length, then convey the wire by transferring it through multiple heading processes, and adds pressure to mold the product into the desired shape. Hamamatsu Tekko has advanced the cold heading process to mass production, achieving net shaping processing (eliminating the need for later cutting).

Low-Temp Gas Soft-NitridingHamamatsu Tekko's gas soft-nitriding is typically |
![]() ![]() |

Hobbing Machine Equipment owned by HAMATETSU VIETNAM Co., Ltd
The latest CNC Dry Cut Hobbing machines have been installed
for machining (creating) gears.
The CNC Dry Cut rapidly and precisely cuts gears while staying environmentally
friendly with machining that does not use cutting oil.
It is capable of cutting gears with a maximum diameter of 150 mm and a maximum
module of 4.